گریدهای فولاد ضد زنگ و کاربرد آنها
دسترسی سریع به محتوای مقاله
تفاوت شرایط سرویس و کاربردی مختلف، مواد متفاوتی را نیز میطلبد. حتی فولادها که آنها را با استحکام و سختی بالا میشناسیم، برای کاربرد در برخی شرایط خاص نظیر محیطهای خورنده و دمای بالا، با چالش مواجه میشوند. درنتیجه، انواع گریدهای فولاد ضد زنگ گسترش داده شدند و امروزه میتوان تأثیر انواع گرید استنلس استیل را در قطعات کوچک و بزرگ و حتی سازههای مهندسی مشاهده کرد. در ادامه به بررسی مهمترین گریدهای استیل ضد زنگ خواهیم پرداخت.
انواع گریدهای فولاد ضد زنگ کدام اند ؟
فولادهای ضد زنگ براساس نوع ریزساختار آنها، به انواع مختلفی تقسیم میشوند که هر یک شامل گریدهای متفاوتی است. تفاوت بین این گریدها به تفاوت در ترکیب شیمیایی آنها مربوط میشود. حضور عناصر آلیاژی متنوع در ساختار انواع گرید استنلس استیل، خواص منحصربهفردی را برای آنها به ارمغان میآورد.
مهمترین انواع فولاد ضد زنگ عبارتاند از:
- فولاد ضد زنگ آستنیتی
- فولاد ضد زنگ فریتی
- فولاد ضد زنگ مارتنزیتی
- فولاد ضد زنگ دو فازی یا داپلکس
- فولاد ضد زنگ رسوب سخت شونده
مهم ترین گریدهای فولاد ضد زنگ
همانطور که در بالا گفته شد، استنلس استیلها به پنج گروه اصلی تقسیم میشوند. هر یک از این گروهها نیز خود شامل گریدهای زیادی هستند که از نظر خواص و کاربرد، متفاوت از یکدیگر هستند. عاملی که نقش مهمی در تعیین این خواص دارد، ریزساختار فولاد است. فولادهای فریتی و آستنیتی دو گرید معروف در این بین هستند که در بازار به استیل بگیر و نگیر معروف اند. در ادامه به معرفی این گریدها میپردازیم.
گریدهای استنلس استیل آستنیتی
استنلس استیل 301
یک فولاد ضدزنگ کروم- نیکل آستنیتی است. این آلیاژ در شرایط آنیلشده غیر مغناطیسی است، اما از طریق کار سرد، مغناطیسی میشود. همچنین، فولاد ضد زنگ 301 میتواند بهآسانی شکل بگیرد و کشیده شود. استحکام بالا و مقاومت عالی در برابر خوردگی، استنلس استیل 301 را برای کاربردهای مختلف شامل قطعات بدنه هواپیما، بدنه تریلر، وسایل آشپزخانه، ترمز خودرو، قالپاق چرخ خودرو، ابزار زه کشی، کابینت، نقاله تسمهای، ظرفشویی، واگنهای مترو و غیره مناسب میکند.
استنلس استیل 302
فولاد ضد زنگ 302 یک گرید بسیار محکم است که مقاومت خوردگی عالی از خود نشان میدهد. استنلس استیل 302 یک گرید غیر مغناطیسی است که با عملیات حرارتی قابل سخت شدن نیست و بهطورکلی، در شرایط آنیلشده استفاده میشود. این نوع گرید، به دلیل سهولت در ساخت و شکلپذیری آن، موردتوجه قرار میگیرد.
استنلس استیل 303
استیل 303 یک گرید فولاد ضد زنگ آستنیتی و غیر مغناطیسی است که توسط عملیات حرارتی قابل سخت شدن نیست. استنلس استیل 303 شامل مقدار قابلتوجهی گوگرد است و بهطور خاص بهمنظور بهبود قابلیت ماشینکاری طراحی شده است. بااینحال، به علت وجود گوگرد در ترکیب این نوع فولاد، خواصی مانند مقاومت در برابر خوردگی و خواص مکانیکی حفظ میشوند.
از طرفی، افزودن گوگرد، مقاومت ورق فولادی 303 را نسبت به آلیاژ 304 کاهش میدهد. همانند سایر گریدهای فولاد آستنیتی، آلیاژ 303 سفتی عالی را نشان میدهد اما وجود گوگرد کمی آن را کاهش میدهد. آلیاژ 303 اغلب در مواردی کاربرد دارد که قطعات بهشدت ماشینکاری میشوند. از مهمترین کاربرهای استیل 303 میتوان به ساخت پیچ و مهره، اتصالات هواپیما، دندهها، پیچها، شفت و غیره اشاره کرد.
استنلس استیل 304
یکی از رایجترین انواع گریدهای فولاد ضد زنگ آستنیتی است که تحت عنوان فولاد ضد زنگ 8-18 نیز شناخته میشود. این نام بر وجود حداقل 18 درصد کروم و 8 درصد نیکل در ساختار این نوع استیل اشاره دارد. به دلیل محتوای بالای کروم و نیکل در این گرید، در هنگام ساخت تجهیزات فرآیندهای شیمیایی، صنایع غذایی و لبنی و آشامیدنی، انتخابی مناسب است. همچنین، این گرید دارای ترکیبی عالی از استحکام، مقاومت در برابر خوردگی و قابلیت ساخت است.
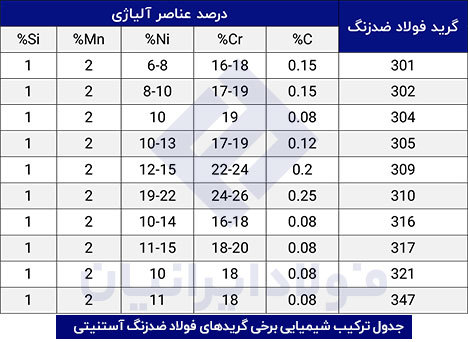
استنلس استیل 305
گرید 305 یک فولاد ضد زنگ آستنیتی کروم- نیکل، با نرخ پایین سختکاری به علت افزایش محتوای نیکل است. این میزان کم از سختکاری باعث میشود که این گرید برای کاربردهای کشش عمیق چند مرحلهای که بدون فرآیند آنیلکردن همراه است، مناسب باشد. نوع 305 در شرایط آنیلشده غیرمغناطیسی است و دارای مقاومت در برابر خوردگی مشابه فولاد ضد زنگ 304/304L است.
استنلس استیل 308
فولاد ضد زنگ 308 معمولاً شامل حدود 20 درصد کروم و بهطور متوسط 11 درصد نیکل است. استنلس استیل 308 اغلب در تجهیزات رستوران و تجهیزات ریختهگری، مخازن شیمیایی و در تولید سیم جوش استفاده میشود.
استنلس استیل 309
فولاد زنگ نزن آستنیتی گرید 309 معمولاً برای کاربردهای دمای بالا استفاده میشود. محتوای بالای کروم و نیکل آن، مقاومت در برابر خوردگی قابلتوجه، مقاومت برتر در برابر اکسیداسیون و استحکام بالاتری را نسبت به گرید 304 برای آن به ارمغان میآورد. این آلیاژ در شرایط بارگذاری غیرتناوبی، تا دمای 1900 درجه فارنهایت (1038 درجه سانتیگراد) در برابر اکسیداسیون مقاومت میکند اما چرخه حرارتی مکرر مقاومت اکسیداسیون را تا حدود 1850 درجه فارنهایت (1010 درجه سانتیگراد) کاهش میدهد.
استنلس استیل 309 به دلیل داشتن کروم بالا و مقدار نیکل کم، میتواند در اتمسفرهای حاوی گوگرد تا دمای 1832 درجه فارنهایت (1000 درجه سانتیگراد) استفاده شود. این آلیاژ برای استفاده در اتمسفرهای بسیار کربوردار توصیه نمیشود زیرا فقط مقاومت متوسطی در برابر جذب کربن از خود نشان میدهد.
آلیاژ 309 را میتوان در کاربردهای کمی اکسیدکننده، نیتریدینگ، سیمانکاری و چرخه حرارتی مورداستفاده قرار داد، به شرطی که حداکثر دمای سرویس کاهش یابد. استیل 309S نوع کمکربن گرید 309 است که برای سهولت در تولید استفاده میشود. نوع 309H نیز گرید پرکربن استیل 309 است و برای کاربردهای مقاوم به خزش در دمای بالا به کار برده میشود.
استنلس استیل 310
استیل 310 یکی دیگر از گریدهای فولاد ضد زنگ آستنیتی است که در دمای بالا، خواص عالی با قابلیت جوشپذیری و شکلپذیری بسیارخوب را ارائه میکند. فولاد ضد زنگ 310 بهطورمعمول برای مواردی که در دمای بالا مورداستفاده قرار میگیرند کاربرد دارد.
محتوای کروم و نیکل بالای آن، مقاومت در برابر خوردگی، مقاومت عالی در برابر اکسیداسیون و مقاومت در دمای بالا تا 2100 درجه فارنهایت را فراهم میکند. با توجه به محتوای بالای کروم و نیکل، این نوع گرید در بیشتر محیطها نسبت به فولاد ضدزنگ 304 یا 309 برتری دارد. نوع کمکربن استیل 310 بهصورت 310S و نوع پرکربن آن بهصورت 310H نشان داده میشوند.
استنلس استیل 314
گرید فولاد ضد زنگ 314 دارای ویژگیهایی مانند مقاومت بالا در دمای بالا در میان سریهای فولاد کروم- نیکل است. محتوای سیلیکون در این ماده باعث بهبود اکسیداسیون و مقاومت در برابر خوردگی میشود. بااینحال، وقتی مدت زیادی در دمای 649- 816 درجه سانتیگراد قرار میگیرد، بسیار شکننده میشود.
استنلس استیل 316
این گرید ضد زنگ دارای 18 درصد کروم، 14 درصد نیکل و مولیبدن است. این ترکیبها مقاومت فولاد را نسبت به خوردگی افزایش میدهند. بهطور خاص، مولیبدن برای کنترل ناحیه خوردگی فلزات مورداستفاده قرار میگیرد. این نوع فولاد در برابر حرارت تا 1600 درجه فارنهایت مقاومت میکند. استیل گرید 316 در صنایع شیمیایی، صنایع کاغذ و خمیرکاغذ، پردازش و توزیع مواد غذایی و نوشیدنی، محیطهای خورندهتر و صنایع دریایی به دلیل مقاومت در برابر خوردگی استفاده میشود. با تفاوت استیل 304 و 316 در این لینک آشنا شوید.
استنلس استیل 317
استیل گرید 317 حاوی درصد بالایی مولیبدن است که این مقدار بیش از محتوای مولیبدن 316 است و در محیطهای بسیار خورنده استفاده میشود. محتوای مولیبدن این گرید به بیش از 3 درصد میرسد. گرید 317 معمولاً در سیستمهای اسکرابر دستگاههای کنترل آلودگی هوا کاربرد دارد که برای حذف ذرات و یا گاز از جریانهای اگزوز صنعتی استفاده میشود.
استنلس استیل 321
استیل گرید 321 حاوی تیتانیوم در حدود حداقل پنج برابر میزان کربن است. این افزودنی برای کاهش یا حذف رسوب کربن کاربیدی است که حاصل جوشکاری فولاد ضد زنگ یا قرار گرفتن آن در معرض دمای بالا است. کاربرد اصلی فولاد ضد زنگ 321 در صنعت هوافضا است.
استنلس استیل 347
فولاد ضد زنگ 347 در شرایط بسیار اکسیدکننده، مقاومت در برابر خوردگی بالاتری نسبت به فولاد ضد زنگ 321 دارد. گرید 347 برای کاربردهایی مورداستفاده قرار میگیرد که چرخه حرارتی بین 800 تا 1650 درجه فارنهایت اعمال میشود.
استنلس استیل 348
گرید 348 یک فولاد ضد زنگ آستنیتی است که مقاومت عالی در برابر خوردگی بیندانهای دارد. این آلیاژ در مواردی مورداستفاده قرار میگیرد که به تحمل چرخه حرارتی بین 800 تا 1650 درجه فارنهایت نیاز است. این آلیاژ در برابر خوردگی جوی، مواد غذایی، محلولهای استریلیزه، بسیاری از مواد شیمیایی آلی و غیر آلی و رنگدانهها مقاومت خوبی میکند. همچنین، به علت کمبود عنصر نیوبیم و تانتالیم در آن، گرید 348 باید برای برنامههای هستهای موردتوجه قرار گیرد.
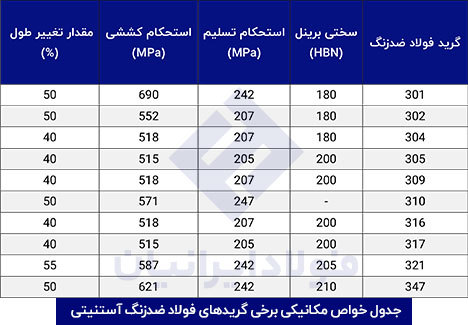
گریدهای استیل ضد زنگ فریتی
استنلس استیل 405
این گرید دارای محتوای کروم کم همراه با آلومینیوم است. این ترکیب شیمیایی به هنگام سرد شدن در دمای بالا از سخت شدن جلوگیری میکند. از فولاد ضد زنگ 405 در ساخت مبدلهای حرارتی استفاده میشود.
استنلس استیل 409
استیل 409 یکی از گریدهای فولاد ضد زنگ فریتی کروم- تیتانیم با مقدار کم کروم و نیکل است. کاربرد اصلی این گرید در سیستم اگزوز خودرو است. مقدار کروم فولاد ضد زنگ 409 در حدود 11 درصد است که کمترین میزان برای تشکیل لایه محافظ ضد زنگ در این نوع فولادها است.
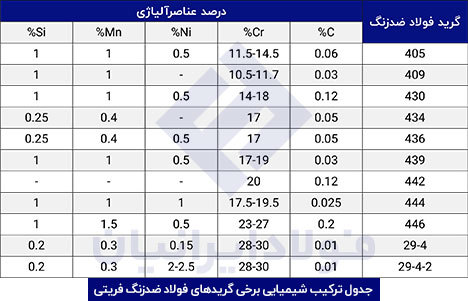
استنلس استیل 430
فولاد ضد زنگ 430 ترکیبی از مقاومت به خوردگی مناسب توأم با شکلپذیری و داکتیلیته خوب را ارائه میدهد. استیل فریتی گرید 430 دارای مقاومت به خوردگی کمتر نسبت به نوع 304 است. بااینحال، این گرید دارای مقاومت مناسب در برابر مواد خورنده مانند اسید نیتریک، گازهای سولفور و بسیاری از اسیدهای آلی و مواد غذایی است.
استنلس استیل 434
گرید 434 پرکاربردترین نوع استنلس استیل در بین گریدهای فریتی غیر سخت شونده است. این گرید دارای محتوای مولیبدن بالا است که باعث بهبود مقاومت در برابر خوردگی آن میشود. کاربردهای معمول این نوع فولاد شامل استفاده در بخش ساختاری خودرو و اتصالدهندهها است.
استنلس استیل 436
گرید 436 درواقع نوع بهبود داده شده از گرید 430 است که نیوبیم و مولیبدن به آن اضافه شده است تا تمایل به تشکیل خطوط مواج در طول شکلدهی در آن کاهش یابد. همچنین، این گرید از مقاومت در برابر خوردگی و جوشپذیری بهتری برخوردار است.
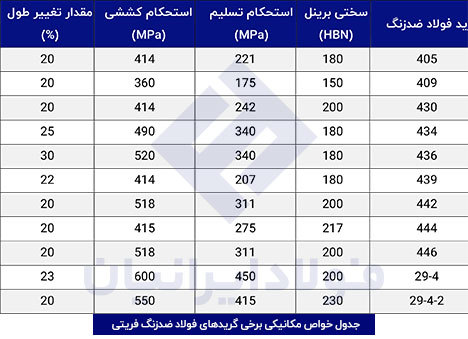
گریدهای فولاد زنگ نزن مارتنزیتی
استنلس استیل 410
فولاد ضد زنگ گرید 410 یک استیل مارتنزیتی با مقدار کروم در حدود 12 درصد است که مقاومت به خوردگی خوبی نیز دارد. بااینحال، مقاومت به خوردگی فولادهای گرید 410 را میتوان با یک سری فرآیندها مانند سختکاری، تمپر کردن و پرداخت بیشتر، افزایش داد. کوئنچ و تمپر میتواند استنلس استیل گرید 410 را سخت کند. آنها بهطورکلی برای کاربردهایی که شامل خوردگی خفیف، مقاومت در برابر حرارت و استحکام بالا هستند استفاده میشوند.
استنلس استیل 416
استیل گرید 416 یک فولاد ضد زنگ با قابلیت ماشینکاری بسیارخوب است بهطوریکه بیشترین قابلیت ماشینکاری را در بین تمام فولادهای ضد زنگ دارا است. قابلیت ماشینکاری را میتوان با افزودن گوگرد بهبود بخشید که منجر به تشکیل آخالهای سولفید منگنز میشود. افزودن گوگرد همچنین شکلپذیری، جوشپذیری و مقاومت در برابر خوردگی فولادهای 416 را به پایینتر از گرید 410 کاهش میدهد. فولادهای گرید 416 به دلیل قابلیت ماشینکاری بالا و هزینه کم، به شکلهای بسیار سخت شده، سخت شده یا سختنشده در دسترس هستند.
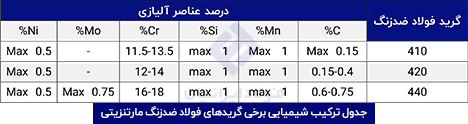
استنلس استیل 420
فولاد ضد زنگ گرید 420 نوعی استنلس استیل با کربن بالا و حداقل 12 درصد کروم است. این گرید در بین تمام گریدهای فولادهای ضد زنگ با 12 درصد کروم، دارای بالاترین سختی به میزان 50 HRC است.
استنلس استیل 431
فولادهای زنگ نزن گرید 431 از نوع مارتنزیتی و قابل عملیات حرارتی هستند. از مهمترین خواص این گرید میتوان به مقاومت در برابر خوردگی عالی، قدرت گشتاور، چقرمگی بالا و خواص کششی خوب اشاره کرد. همه این ویژگیها آنها را برای کاربردهایی نظیر پیچ و شفت ایدئال میکند. بااینحال، این فولادها به دلیل استحکام تسلیم بالایی که دارند، نمیتوانند کارسرد شوند. ازاینرو برای عملیاتی مانند کشش عمیق، خمش یا شکلدهی چرخشی مناسب هستند.
استنلس استیل 440
فولادهای زنگ نزن گرید 440 فولادهای با کربن بالا هستند که پس از عملیات حرارتی به بالاترین سختی، مقاومت در برابر سایش و استحکام نسبت به تمام گریدهای فولاد ضد زنگ میرسند. این ویژگیها این گرید را برای کاربردهایی مانند اجزای شیر، یاتاقان و ساخت چاقو مناسب میکند. با فولاد مناسب ساخت چاقو در این لینک آشنا شوید.
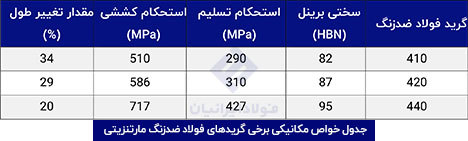
گریدهای فولاد ضد زنگ داپلکس (دو فازی)
استنلس استیل 2205
استیل 2205 برای محیطهای با فشار و خوردگی بالا، بسیار مناسب است. این فولاد همچنین دارای خواص خستگی بسیارخوب و همچنین انبساط گرمایی کمتر و رسانایی گرمایی بالاتر از گریدهای آستنیتی است. استفاده از این گرید باید به زیر دمای 315 درجه سانتیگراد محدود شود، زیرا افزایش شدید درجه حرارت میتواند موجب شکننده شدن آن شود.
استنلس استیل 2304
فولاد ضد زنگ 2304 دارای مقاومت در برابر خوردگی در حدود گریدهای آستنیتی 304 و 316 است، اما مقدار استحکام تسلیم آن تقریباً دو برابر نقطه تسلیم گریدهای یادشده است. این گرید برای استفاده در دمای بین منفی 50 تا 300 درجه سانتیگراد مناسب است. ضمن اینکه، استیل گرید 2304 دارای مقاومت بالا در برابر ترکخوردگی و نیز دارای قابلیت جوشپذیری خوب و ماشینکاری مناسب است.
استنلس استیل 2507
استنلس استیل 2507 یک فولاد ضد زنگ سوپرداپلکس است. این فولاد در مواردی استفاده میشود که به استحکام استثنایی و مقاومت در برابر خوردگی خیلی خوب نیاز است. مواردی همچون فرآیند شیمیایی، پتروشیمی و ساخت تجهیزات دریایی ازجمله کاربردهای این نوع فولاد ضد زنگ است. این گرید دارای مقاومت عالی در برابر ترکخوردگی، هدایت حرارتی بالا و ضریب انبساط حرارتی پایین است. سطوح بالای کروم، مولیبدن و نیتروژن در این گرید، مقاومت زیادی در برابر خوردگی ناحیهای، شکافی و خوردگی یکنواخت ایجاد میکند.
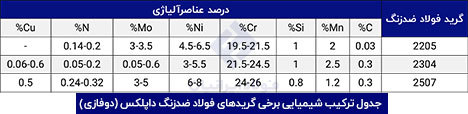
گریدهای استیل ضد زنگ رسوب سخت شونده(PH)
استنلس استیل 4-17
آلیاژ 4-17 یک فولاد ضدزنگ رسوب سخت شونده کروم- مس است که برای کاربردهای با استحکام بالا و سطح متوسط از مقاومت در برابر خوردگی فلزات مورداستفاده قرار میگیرد. این گرید دارای استحکام بالا و مقاومت در برابر خوردگی در تمام شرایط حرارتی است. استیل 4-17 را میتوان در درجه حرارتهای مختلف تحت عملیات حرارتی قرار داد. این گرید نباید در دمای بالاتر از 300 درجه سانتیگراد یا درجه حرارت بسیار پایین استفاده شود.
استنلس استیل 5-15
این گرید درواقع مشابه با 4-17 و برای چقرمگی بیشتر نسبت به 4-17 طراحی شده است. فولاد ضد زنگ 5-15 در مواردی استفاده میشود که به مقاومت در برابر خوردگی بیشتری در مقایسه با سایر گریدهای مارتنزیتی مشابه نیاز است.
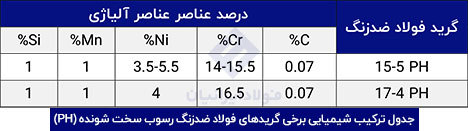
انواع گرید های فولاد ضد زنگ در یک نگاه
شکل زیر انواع گرید فولاد ضد زنگ و نحوه ساخت آنها را به طور خلاصه و مختصر نشان می دهد.
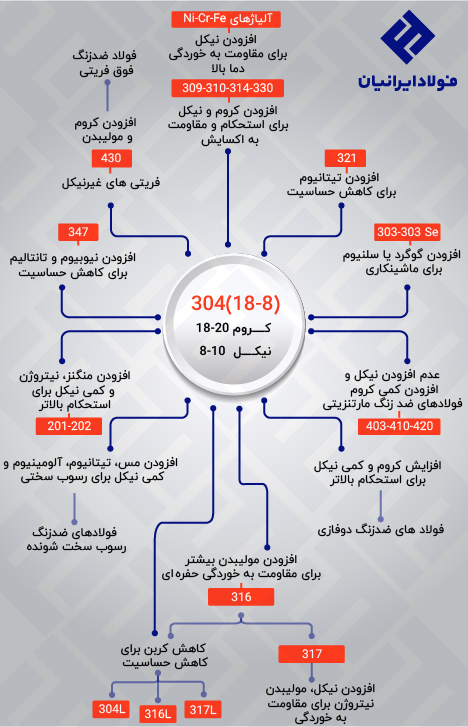
سؤالات متداول
1- پرکاربردترین گرید فولاد ضد زنگ کدام است؟
گریدهای 304 و 316 در بین تمام گریدهای استنلس استیل بیشترین کاربرد را دارند.
2- کدام گریدهای استنلس استیل برای کاربردهای دما بالا مناسباند؟
انواع استیلهای 309، 310، 304 و 316 بدین منظور مناسباند.
3- مقاومترین گرید فولاد ضد زنگ کدام است؟
انواع گریدهای مارتنزیتی و رسوب سخت شونده در بین تمام فولادهای ضد زنگ بیشترین استحکام را دارند.