آهن چیست ، اسرار این فلز شگفت انگیز
دسترسی سریع به محتوای مقاله
به اطراف خود بنگرید! چه تعداد ابزار یا وسیله در اطراف شما است که از آهن ساختهشدهاند؟ آیا میتوانید ردپای این فلز را در زندگی روزمره و حتی صنایع مختلف بیابید؟ پاسخ کوتاه و روشن است: بله! درواقع باید پرسید آیا صنعتی وجود دارد که در آن از آهن استفاده نشده است؟ همین چند جمله برای بیان اهمیت استفاده از آهن بهعنوان مهمترین فلز شناختهشده توسط بشر کافی است. اما این فلز چگونه به این شهرت و اهمیت رسیده است؟ آهن چیست و چگونه کشف شد؟ چه خواصی سبب برتری آهن نسبت به دیگر فلزات شدهاست؟
در وصف اهمیت آهن و کاربرد آهن میتوان گفت که همچون آب که مایه حیات است، قلب صنایع مختلف نیز از وجود آهن به تپش درمیآید. این فلز که پس از آلومینیوم، فراوانترین عنصر در پوسته زمین است، آنقدر در زندگی بشر دخیل بوده و هست که یک دوره را به نام آن نام نهادهاند یعنی عصر آهن. در ادامه این مقاله به بررسی سرنوشت این فلز میپردازیم، اینکه چگونه کشف شد، چگونه به کاربردهای مختلف آن پی بردند و چگونه در صنایع مختلف و حساس به کار برده شد. به منظور اطلاع از قیمت روز آهن آلات به این لینک مراجعه نمایید.
آهن چیست ؟
احتمالا این پرسش که آهن چیست، دیگر منسوخ شده باشد و همه با شنیدن نام آن، به یاد یک فلز محکم و قهوه ای رنگ میافتند. بااینحال، این واژه از کجا آمده است؟ آهن یا Iron که نام آنگلوساکسون (قبایلی از ژرمنها که در محدوده انگلستان کنونی میزیستند) آن، Iren است، دارای نماد شیمیایی Fe است که از عبارت لاتین Ferrum گرفتهشده است.
برخی نیز معتقدند که معنی واژه آهن به "فلز مقدس" اشاره دارد؛ چراکه در گذشته جزو اولین موادی بود که با آن انواع سلاحهای مستحکم را ساختند. این فلز با عدد اتمی 26، در رده چهارم و گروه هشتم از جدول تناوبی قرار دارد. چگالی آهن 7.87 گرم بر سانتیمتر مکعب است و بنابراین در دسته فلزات نسبتاً سنگین اما با استحکام بالا قرار میگیرد.
تاریخچه آهن
مورخان معتقدند که مصریان اولین مردمی بودند که در حدود پنج یا شش هزار سال پیش با مقادیر کمی از آهن کارکردند. فلزی که آنها استفاده کردند، ظاهراً از شهابسنگها استخراج شده است. شواهدی ازآنچه گمان میرود اولین نمونه از استخراج و ذوب آهن باشد، به فرهنگ باستانی هیتی ها در ترکیه کنونی اشاره دارد.
ازآنجاکه آهن مادهای بسیار برتر برای ساخت سلاح و ابزار نسبت به سایر فلزات شناختهشده بود، از فرآیند تولید آن همچون یک راز کاملاً محافظت میشد. بااینحال، تکنیک اصلی ساخت آن ساده بود و استفاده از آهن بهتدریج گسترش یافت. همانطور که آهن در مقایسه با مواد دیگر مفید بود، معایبی نیز داشت.
کیفیت ابزارهای ساختهشده از آن، بسته به منطقهای که سنگآهن از آن استخراج میشد و روش استخراج آهن، بسیار متغیر بود. ماهیت شیمیایی تغییراتی که در طول استخراج آهن اتفاق میافتد نیز تا آن زمان درک نشده بود. بهویژه اینکه، تا آن زمان هنوز به اهمیت کربن در قابلیت سخت شدن آهن به عنوان یک فاکتور کلیدی پی برده نشده بود. حال با شناخت این فلز، به نظر شما مهم ترین خواص آهن چیست که آن را تا این حد ارزشمند کرده است؟
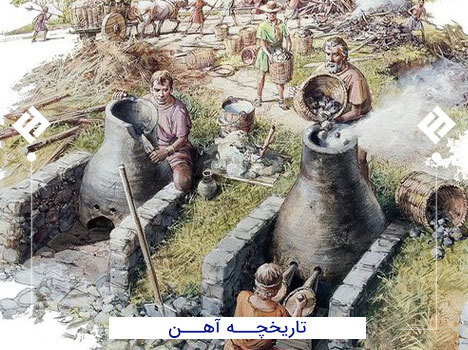
خواص آهن
آهن به سبب خواص منحصربهفرد خود، کاربردهای گستردهای در صنایع مختلف پیدا کرده است. این خواص بهقدری مفید و کاربردی هستند که باوجود روی کار آمدن مواد پیشرفتهای چون کامپوزیتها، نانو مواد، سوپرآلیاژها و غیره، هنوز هم آهن انتخاب اول صنایع مختلف برای ساخت قطعات فلزی است. البته امروزه شکل دیگری از آهن بهجای آهن خالص کاربرد دارد و آن فولاد است که از افزودن کربن تا مقدار 2.1 درصد به آهن به دست میآید. تفاوت آهن و فولاد را در این لینک بخوانید.
مهم ترین خواص آهن عبارتاند از:
- قابلیت آلیاژسازی و تولید فولاد
- خاصیت مغناطیسی
- نرم و قابلانعطاف
- قابلیت چکشخواری
- کمهزینه و در دسترس
- رسانایی
- استحکام بالا
ساختار آهن
آلوتروپ آهن چیست؟ آیا آهن انواع مختلفی دارد؟ آهن در دماهای مختلف، ساختارهای کریستالی متفاوتی دارد. بدین معنی که در فشار 1 اتمسفر، با افزایش دما، شبکه بلوری آن تغییر میکند. این امر منجر به پیدایش آلوتروپ های (دگرشکل) آهن میشود. این ویژگی خاص، دلیل خاصیت مغناطیسی آهن و نیز قابلیت تبدیلشدن آن به فولاد است.
این فلز در زیر دمای 727 درجه سانتیگراد، دارای ساختار کریستالی مکعبی مرکز پر (Body Centered Cubic) یا بهاختصار BCC است. این نوع آهن را آهن آلفا میگویند. در بالای دمای 727 و تا دمای 912 درجه سانتیگراد، ساختار کریستالی آهن به مکعبی مرکز وجوه پر (Face Centered Cubic) یا FCC تبدیل میشود که آهن گاما نام دارد. این ساختار نیز تا دمای 1394 درجه سانتیگراد پایدار است و در بالای این دما نیز مجدداً به BCC تبدیل میشود و که همان آهن دلتا است.
در بین این سه فاز از آهن، فاز گاما مهمترین آن است که استفاده فراوانی نیز از آن میشود. بهمنظور عملیات حرارتی فولادها، آنها را تا تبدیلشدن به ساختار FCC حرارت میدهند که اصطلاحاً آستنیته کردن نام دارد. سپس با سرعتهای سرمایش مختلف، ریزساختارهای متفاوتی برای فولاد قابلدستیابی است. بهمنظور آشنایی با انواع عملیات حرارتی فولادها به این لینک مراجعه نمایید.
همچنین، آهن در گستره دمایی بالای 770 درجه سانتیگراد، خاصیت مغناطیسی خود را از دست میدهد. به این آهن که در گستره دمایی 770 تا 910 درجه سانتیگراد خاصیت مغناطیسی ندارد، آهن بتا نیز گفته میشود. دمای 770 درجه به دمای کوری آهن (Curie Temperature) معروف است که در آن، آهن فرومغناطیس به آهن پارامغناطیس تبدیل میشود.
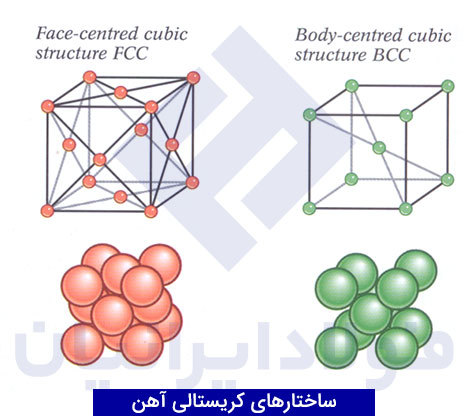
انواع سنگ آهن
سنگآهن بهصورت ترکیبات مختلفی وجود دارد. رایجترین کانیهای اکسیدی از آهن و کانیهایی که در پوسته زمین وجود دارند عبارتاند از:
- هماتیت قرمز (Fe2O3)
- هماتیت قهوهای یا لیمونیت (2Fe2O3.3H2O)
- مگنتیت (Fe3O4)
- سیدریت (FeCO3)
- پیریت (FeS2)
دراینبین، هماتیت حدود 40 تا 60 درصد آهن داشته و مقدار گوگرد و فسفر آن نیز از دیگر کانیهای آهن کمتر است. مگنتیت نیز حدود 60 تا 70 درصد آهن دارد و این مقدار در سیدریت به 30 تا 40 درصد میرسد. از پیریت برای آهن سازی استفاده نمیشود و صرفه اقتصادی ندارد. پیریت به دلیل ظاهری طلایی، به طلای احمقها معروف است!
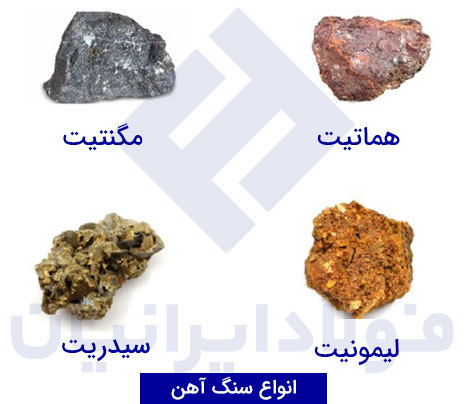
فرآیند تولید آهن
هدف اصلی در تولید آهن، رهاسازی آهن از پیوند شیمیایی با اکسیژن است و ازآنجاییکه کوره بلند کارآمدترین فرآیند است، در اینجا بیشترین توجه را به خود جلب میکند. روشهای جایگزینی که بهعنوان احیای مستقیم (Direct Reduction) شناخته میشوند در بسیاری از کشورها استفاده میشوند، اما کمتر از 5 درصد آهن از این طریق ساخته میشود. گروه سوم از تکنیکهای آهنسازی که بهعنوان احیای ذوبی (Smelting Reduction) طبقهبندی میشوند، هنوز در مراحل ابتدایی هستند. بهترین روش از بین روش های موجود برای تولید آهن چیست؟ کدام روش بهصرفهتر است؟
تولید آهن به روش کوره بلند
آهن از طریق احیای کربن در کوره بلند تولید میشود. سنگآهن (هماتیت Fe2O3)، کک و سنگ آهک (CaCO3) (معمولاً به نسبت 1:4:8) از بالای کوره به داخل آن شارژ میشوند. پسازآن، از سوراخهایی نزدیک به پایین محفظه، هوای داغ وارد میشود و یک انفجار اتفاق میافتد که باعث سوزاندن کک و دیگر مواد شارژ شده میشود. سوزاندن کک باعث تولید گرما در حدود 2000 درجه سانتیگراد میشود. با سوزاندن کک، مونوکسید کربن تولید میشود که به سمت بالا حرکت کرده و Fe2O3 و FeO را احیا میکند.
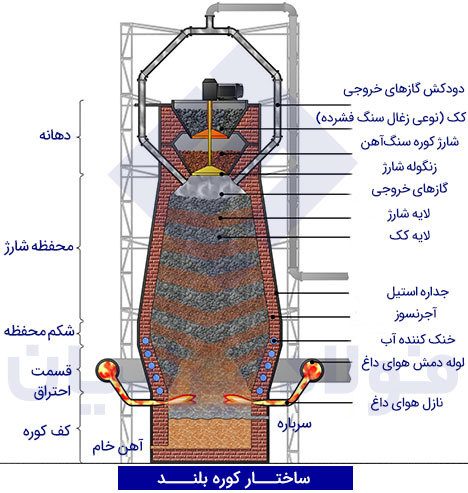
سنگ آهک در حدود 900 درجه سانتیگراد تجزیه میشود و حاصل آن CaO است که با سیلیس ترکیب میشود و سرباره(CaSiO3) را تشکیل میدهد. مونواکسید کربن در ادامه مسیر با FeO واکنش میدهد و حاصل آن، آهن مذاب است که به آن آهن خام یا Pig Iron میگویند. آهن خام حدود 4 درصد کربن، تا 1 درصد فسفر و حدود 0.02 تا 0.08 درصد گوگرد دارد و برای استفاده صنعتی مناسب نیست.
گوگرد یک عنصر همراه نامطلوب است چراکه در سیستمهای ترش حاوی گاز H2S، سبب ایجاد ترک و نشت گاز میشود. بنابراین، عملیات سولفورزدایی توسط سودا یا کاربید کلسیم انجام میشود تا مقدار گوگرد کاهش یافته و در حد هزارم درصد برسد. از طریق فسفرزدایی نیز میتوان درصد فسفر موجود در آهن خام را کاهش داد.
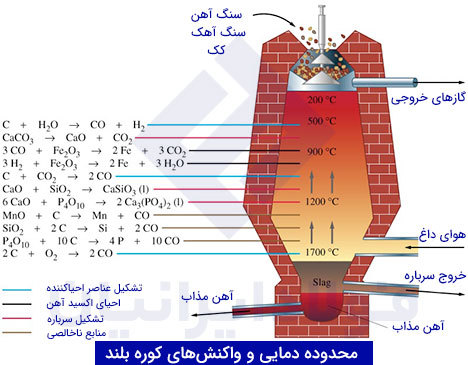
تولید آهن به روش احیای مستقیم
در این فرآیند، از دمایی پایینتر از دمای ذوب سنگآهن و دیگر مواد همراه، بهمنظور تولید آهن استفاده میشود. گانگ (مواد باطله) در محصول اسفنج مانند که آهن اسفنجی نام دارد بهعنوان آهن احیاشده مستقیم (Direct Reduction Iron) یا DRI شناخته میشود، باقی میماند و باید در فرآیند فولادسازی بعدی حذف شود. بنابراین، تنها سنگهای معدنی و گلولههای با عیار بالا ساختهشده از سوپرکنسانتره (حداقل 66 درصد آهن) برای ساخت آهن به روش DR مناسب هستند.
روش احیای مستقیم بیشتر در شرایط خاص استفاده میشود که اغلب به عرضه ارزان گاز طبیعی مرتبط است. این روش شامل چندین فرآیند مبتنی بر استفاده از یک کوره دوار با شیب کم است که در آن سنگ معدن، زغالسنگ و مواد بازیافتی در انتهای بالایی با حرارت تأمینشده توسط یک مشعل نفت یا گاز شارژ میشوند.
بااینحال، نتایج در مقایسه با فرآیندهای مبتنی بر گاز، که بسیاری از آنها در کورههای شفتی انجام میشوند، متوسط هستند. در موفقترین آنها که به نام روش میدرکس (Midrex) شناخته میشود (بخشی از نام توسعهدهنده آن، شرکت Midland-Ross)، یک اصلاحکننده گاز متان (CH4) را به مخلوطی از مونوکسید کربن و هیدروژن تبدیل میکند و این گازها را به نیمه بالایی یک کوره شفت کوچک میفرستد. سپس، مواد در دمای 850 درجه سانتیگراد ازنظر شیمیایی احیا میشوند. بار متالیز شده قبل از تخلیه در نیمه پایینی شفت خنک میشود.
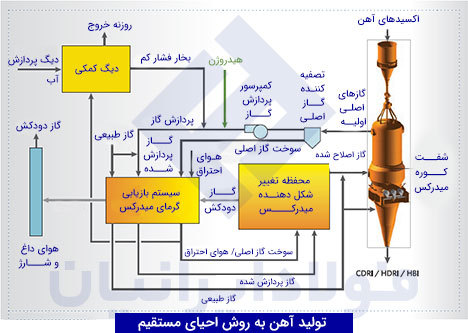
تولید آهن به روش احیای ذوبی
این روش مشابه با روش احیای مستقیم است اما فقط در دو مرحله انجام میشود. کمیاب بودن زغالسنگ کک سازی برای استفاده در کوره بلند و هزینه بالای کورههای کک دو دلیل برای ظهور این فرآیند و جایگزینی آن بهجای دیگر روشهای تولید آهن است. در این روش، بهمنظور احیای ذوب از دو واحد استفاده میشود.
در واحد اول، سنگآهن توسط گازهای خروجی از واحد دوم، که یک ذوب-گازفایر با زغالسنگ و اکسیژن است، گرم شده و احیا میشود. سپس سنگ معدن نیمه احیاشده در واحد دوم ذوب میشود و آهن مذاب تولید میشود. فناوری احیای ذوبی، امکان استفاده از طیف وسیعی از سنگآهنهای ریزودرشت برای تولید آهن ممکن میسازد. همچنین، دیگر مزیت این روش این است که درجایی که امکان استفاده از گاز وجود ندارد، میتوان مستقیماً از کک استفاده کرد.
کاربرد آهن چیست؟
آهن و فولاد عمدتاً در انواع مختلف واحدهای سازهای در تمدن مدرن و مهندسی عمران استفاده میشوند. انواع مختلفی از فولاد با خواص و کاربردهای مختلف وجود دارند که توسط آهن و از طریق آلیاژ شدن با کربن و سایر عناصر شیمیایی ساخته میشوند. شاید امروزه از آهن بهصورت خالص استفاده چندانی نشود و اکثر محصولاتی که آهن دارند، درواقع این عنصر را در قالب انواع فولادها به همراه دارند. استفاده اصلی از آهن در ساخت فولاد و چدن است.
فولاد کربن متوسط بیشترین کاربرد را در پلها، دکلهای برق، زنجیر دوچرخه، ابزارهای برش و لوله تفنگ دارد. همچنین بهعنوان یک کاتالیزور شیمیایی در فرآیند هابر برای تولید آمونیاک استفاده میشود. در تولید هیدروژن در مقیاس کوچک نیز از آن بهعنوان یک عامل کاهنده استفاده میشود.
فولاد ضدزنگ آلیاژ مهمی از آهن است که حاوی حداقل 12 تا 15 درصد کروم و سایر فلزات مانند نیکل، مولیبدن، تیتانیوم و مس است که در برابر خوردگی و اثر اسیدها مقاوم است. این نوع فولادها بهطور گستردهای در ساختوساز، ساخت بلبرینگ، کارد و چنگال، ابزار جراحی پزشکی و جواهرات کاربرد دارند.
چدن آلیاژ دیگری از آهن است که حاوی 2 تا 5 درصد کربن است که بهطور گسترده در لولهها، شیرها، پمپها و تولید آهنربا استفاده میشود.
بازیافت آهن
آهن بهعنوان یک جزء در وسایل نقلیه، بهویژه در آلیاژهای فولادی، از اتومبیل گرفته تا کشتی و هواپیما استفاده میشود. اما آیا آهن قابل بازیافت است؟ پاسخ بله است؛ بازیافت کلیه وسایل آهنی مزایای محیط زیستی زیادی دارد. قابلیت بازیافت آهن و فولاد ازآنجهت اهمیت دارد که بازیافت آنها، هزینه بهمراتب کمتری نسبت به تولید آهن از سنگ معدن دارد. با بازیافت آهن، خواص آن دچار افت نمیشود. ضمن اینکه، فرآیند بازیافت آهن تکرارپذیر است و پس از هر بار بازیافت و استفاده مجدد، دوباره قابلیت بازیافت دارد.
با انجام این کار، بهطور فعال به کاهش استفاده از منابع طبیعی، انتشار کمتر گازهای کربنی و کاهش میزان انرژی موردنیاز برای تولید فلزات بیشتر از سنگ معدن کمک میشود. بهطور دقیقتر، به ازای هر تن آهن و فولاد بازیافتی، میتوان 1.5 تن سنگآهن را ذخیره کرد، انتشار گازهای گلخانهای را تا 86 درصد و آلودگی آب را نیز تا 76 درصد کاهش داد. در همین راستا، به منظور آشنایی بیشتر با فرآیند بازیافت آهن آلات، مقاله آهن قراضه چیست را مطالعه نمایید.
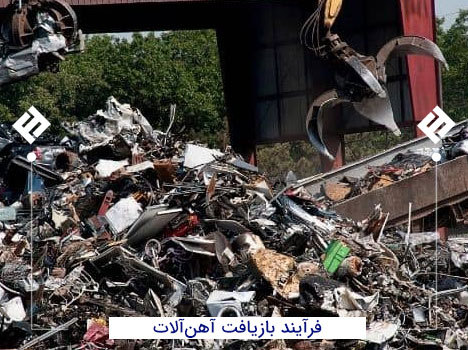
جمع بندی
اکنون می دانیم که آهن چیست و چرا و چگونه به این جایگاه ارزشمند در صنعت و زندگی بشر رسیده است. باوجود پیشرفت تکنولوژی و پیدایش مواد پیشرفته و جدید، استفاده از آهن بهعنوان کاربردیترین فلز برای بشر هیچگاه متوقف نشد. خواص شگفتانگیز این فلز و مهمتر از همه، تولید فولاد از آهن، سبب شده تا آهن همواره مهمترین فلز در صنایع مختلف محسوب شود. هزینه تولید کم، قابلیت بازیافت، استحکام بالا، خواص مغناطیسی و فراوانی، ازجمله دلایل محبوبیت و حیاتی بودن این فلز به شمار میروند.