روش های جوشکاری انواع لوله فولادی
دسترسی سریع به محتوای مقاله
فرایند جوشکاری یکی از مهمترین مراحل در کاربرد لولههای فولادی به شمار میرود که باعث افزایش کارایی این مقاطع در صنایع مختلف میشود. ازاینرو با توجه به تنوع کاربرد لولههای فولادی در صنایع مختلف با توجه به تنوع سیالات، ضخامت، جنس و غیره شاهد هستیم که روشهای جوشکاری لولههای فولادی نیز بسیار متنوع هستند. البته هرکدام از این روشهای جوشکاری برای کاربرد، ضخامت و یک شرایط خاص مناسب هستند که با توجه به نحوه کاربرد، ناحیه جوش متفاوتی ایجاد میکنند. در این مطلب تا حد امکان سعی میکنیم انواع روشهای جوشکاری را با توجه به انواع لوله های فولادی معرفی کنیم.
مراحل جوشکاری لوله های فولادی
مراحل جوشکاری لولههای فولادی شامل موارد زیر است:
1. مشخص شدن مسیر عبور، سایز و جنس لوله
2. انتخاب روش جوشکاری متناسب با کاربرد، جنس، ضخامت و نوع لوله فولادی
3. آماده کردن محل یا مفصل براساس استانداردها مانند استاندارد API 1104 یا ASME برای آمادهسازی مفصل خطوط لوله
4. پاک کردن محل جوش از هرگونه زنگزدگی، رنگ، مواد شیمیایی، گرد و خاک و ... .
5. رعایت نکات ایمنی از چک کردن دستگاه جوش تا پاکسازی محیط اطراف از مواد آتشزا
6. رعایت نکات ایمنی فردی مانند استفاده از کلاه، عینک و دستکش
7. انجام جوشکاری
8. تمیز کردن سطح لولههای فولادی از سرباره جوش
9. تست لولهها برای اطمینان از عملکرد مناسب
10. برطرف کردن ایرادات در صورت نیاز
شناخت انواع لولههای فولادی یکی از مهمترین اطلاعات برای انتخاب روش صحیح جوشکاری است. لوله درزدار و بدون درز دو گروه عمده از انواع لولههای فولادی هستند که در این مقاله میتوانید درباره تفاوت لوله درزدار و بدون درز و مشخصات و کاربردهای هریک بیشتر بخوانید.
انواع روش های جوشکاری لوله های فولادی
روشهای جوشکاری را براساس نحوه اتصال میتوان به انواع زیر تقسیم کرد:
1. جوشکاری به روش اتصال بوشنی جوشی (SW)
2. جوشکاری به روش اتصال پیچی یا رزوهای (Scrd)
3. جوشکاری به روش اتصال جوشی لب به لب (BW)
نکات مهم روش اتصال بوشنی جوشی در لوله فولادی
- از مهمترین روشهای اتصال لولههای فولادی
- استفاده از یک وصله (بوشن) برای اتصال بهتر
- آسان بودن نصب عدم نیاز به خالجوش
- توجه به کوتاه شدن طول لوله به دلیل قرار گرفتن در داخل بوشن
- حداکثری شدن تضمین آببندی در این روش
- مورداستفاده برای لولههای با سایز اسمی 2 اینچ و کوچکتر
- مناسب برای استفاده در خطوط مواد گازی، سمی و اشتعالپذیر
- دقت کردن به معایبی نظیر تله افتادن سیال عبوری و افت فشار
نکات مهم روش اتصال پیچی یا رزوهای در لولههای فولادی
- از انواع روشهای اتصال غیردائمی با امکان جدا کردن قطعات و مونتاژ مجدد
- دارای مراحل نصب ساده با خطر آتشسوزی کمتر
- مناسب برای کاربردهایی با نیاز به قابلیت باز و بسته کردن
- مناسب برای خط لولههای با سایز اسمی 3 اینچ و کمتر
- کم بودن ضریب اطمینان این روش نسبت به سایر روشها
- مورداستفاده در صنایع کماهمیت
نکات مهم روش جوش لب به لب در لوله فولادی
- روش اتصال و جوشکاری لولههای فولادی به روش لب به لب یکی
- از بهترین و اقتصادیترین روشهای اتصال لولههای با سایز اسمی بزرگ
- بیشترین کاربرد برای اتصال لولههایی با سایز 2 اینچ و بیشتر
- نیاز به ماشینکاری و پخ زدن انتهای لوله و لبهی اتصالات
- نیاز به یک فضای خالی 16/1 اینچی در میان دو لبه لوله و پر کردن آن با استفاده از الکترود مذاب
- نیاز به حلقه محافظ برای جلوگیری از ورود مواد مذاب
- نیاز به خالجوش برای ثابت نگهداشتن و تنظیم زاویه
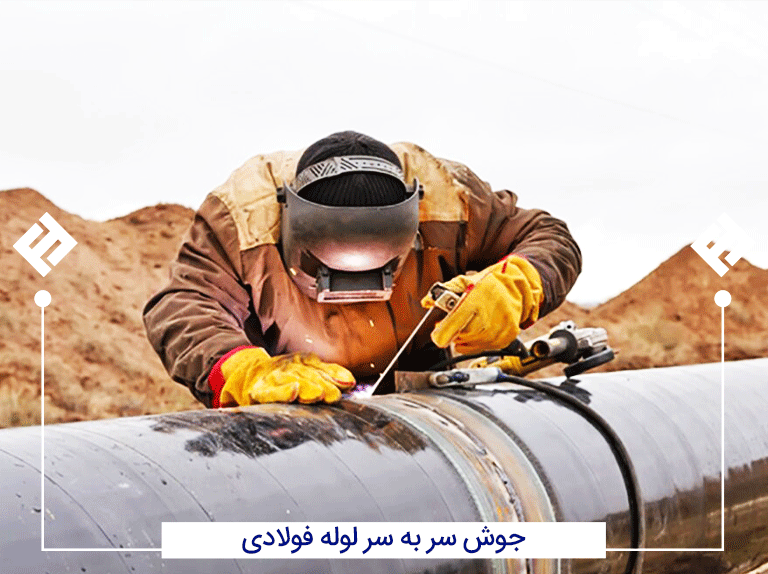
انواع روش های جوشکاری براساس نوع فرآیند
انواع روشهای جوشکاری برحسب نوع فرآیند شامل موارد زیر است:
1. روشهای جوشکاری ذوبی
2. روشهای جوشکاری حالت جامد یا غیر ذوبی
انواع روشهای جوشکاری ذوبی در لوله فولادی
یکی از اصلیترین کاربردهای لولههای فولادی انتقال سیالات نظیر آب، گاز، روغن و ... است. انواع روشهای جوشکاری الکتریکی برای اتصال لولههای فولادی شامل موارد زیر میشود:
1. جوشکاری قوسی توپودری (Flux-Cored Arc Welding)
2. جوشکاری قوسی زیر پودری (Submerged Arc Welding)
3. جوشکاری قوسی با الکترود روکشدار (Shielded Metal Arc Welding)
4. جوشکاری قوسی الکترود فلزی تحت پوشش گاز محافظ (Gas Metal Arc Welding) یا MIG/MAG
5. جوشکاری قوسی با الکترود تنگستن (Gas Tungsten Arc welding) یا TIG
نکات جوشکاری قوس توپودری (Flux-Cored Arc Welding)
- نیاز به دستگاههای نیمه اتوماتیک
- سرعت و بهرهوری بالاتر نسبت به روش GMAW
- عدم نیاز به گاز محافظ خارجی
معایب:
- دارای نرخ رسوب کمتر نسبت به جوشکاری قوسی با محافظ گازی
- احتمال به وجود آمدن اخلال در گاز محافظ با شروع وزش باد و ایجاد تخلخل در جوش
نکات جوشکاری قوس زیر پودری (Submerged Arc Welding)
- دارای بالاترین راندمان رسوبگذاری در مقایسه با سایر روشهای جوش کاری
- دارای سطوح جوشکاری سالم و بدون نقص
- عدم وجود هیچ سرباره پرتابی یا گاز جوشکاری و دارای ایمنی بالای
- دارای سرعت بالا در اجرا
- عدم نیاز به تعویض الکترود
- عدم وابستگی به مهارت بالای جوشکار
معایب:
- ردیابی دشوار به دلیل قوس نامرئی
- گران بودن هزینه جوشکاری نسبت به سایر روشها
- اجرای جوشکاری تنها در وضعیت تخت یا 1G
- مشکل در حملونقل تجهیزات
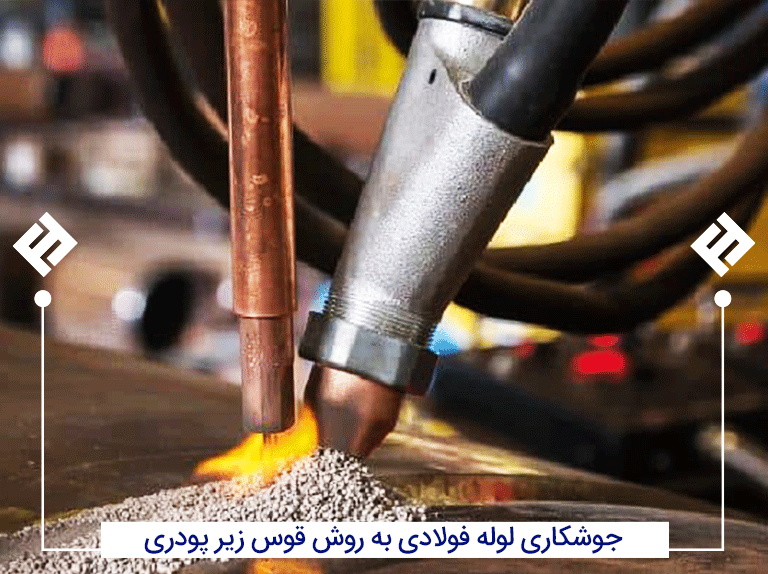
نکات مهم در جوش کاری لوله فولادی با الکترود روکشدار (SMAW)
- ایجاد اتصال توسط گرمای تولید شده توسط قوس الکتریکی
- انتخاب تعداد پاس جوشکاری براساس ضخامت لوله، موقعیت جوشکاری، اندازه الکترود و جریان مورداستفاده
- معمولاً یک پاس برای هر 8/1 اینچ (3.2 میلیمتر) ضخامت لوله
- قطر الکترود مور استفاده از 8/1 اینچ تا 3.16 اینچ (3.2 میلیمتر تا 4.8 میلیمتر)
- در مقاطع ضخیم قطعه کار بهعنوان قطب مثبت و الکترود بهعنوان قطب منفی
- در مقاطع نازک، الکترود بهعنوان قطب مثبت و قطعه کار بهعنوان قطب منفی
- امکان جوشکاری در همه حالتها شامل 1G، 2G، 3G و ...
- دارای تجهیزات جوشکاری ساده و قابلحمل
- عدم نیاز به گازهای شار یا محافظ
معایب:
- سرعت اجرای پایین و مقرون بهصرفه نبودن
- دستی بودن فرآیند جوشکاری
- وابستگی کیفیت جوش به مهارت جوشکار
- عدم یکنواختی در جوش به دلیل تعویض الکترود
- نیاز به صرف زمان و هزینه برای تمیز کردن سرباره
نکات مهم جوش کاری لوله فولادی با الکترود فلزی تحت پوشش گاز (GMAW)
- شناخته شدن با نام MIG یا جوشکاری گاز خنثی- فلز
- نیاز به کنترل دقیق متغیرهای جوشکاری برای افزایش بهرهوری و کیفیت
- دارای راندمان بالای رسوبدهی (90 تا 97 درصد) و تولید اندک دود
- عدم نیاز به مهارت جوشکار
- دارای الکترود از نوع مصرفی و گاز محافظ هلیوم یا آرگون و (گاز کربن دیاکسید در ایران)
- کاربرد در تعمیر خودرو، لولهکشی و صنایع دریایی
- دارای جوش تمیز با قدرت تحمل بالا
- اجرای جوشکاری در تمام وضعیتهای 1G، 2G، 3G و ...
- عدم نیاز به تمیزکاری پس از کار
معایب:
- گران بودن فرآیند
- حساس به وزش باد
- نیاز به تجهیزات نیمه اتوماتیک / اتوماتیک و بالا بودن هزینه جوشکاری
نکات مهم جوشکاری قوسی با الکترود تنگستن (Gas Tungsten Arc welding)
- شناخته شدن با عنوان جوشکاری TIG
- مناسب برای اتصالات مهم با نیاز به جوش دقیق
- دارای نرخ رسوب کمتر
- نیاز به گاز محافظ آرگون
- استفاده از یک فلز بهعنوان ماده پر کننده
- مورداستفاده برای اتصال بخشهای ضخیم استیل یا فلزات غیر آهنی
- تمرکز حرارت بالا
- عدم نیاز به تمیزکاری پس از پایان کار
معایب:
- دارای هزینه تجهیزات بالا نسبت به سایر روشها
- احتمال دفورمه شدن فلز در اثر حرارت بیش از حد
- حساس به وزش باد
- احتمال شکسته شدن نوک نیز الکترود و آلوده شدن حوضچه مذاب با الکترود تنگستنی
نکته: به هر بار اتصال الکترود مصرفی یا غیر مصرفی در نطقه اتصال پاس جوش و یا Weld Pass میگویند.
انواع روشهای جوشکاری لولههای فولادی انتقال سوخت
معمولاً از روشهای زیر برای جوشکاری لولههای فولادی انتقال سوخت استفاده میکنند:
- روش جوشکاری با قوس الکتریکی و استفاده از فلاسک هادی (پودرهای هادی)
- روش جوشکاری دستی با قوس الکتریکی و الکترودهای پوششدار
- روش جوشکاری با قوس الکتریکی و استفاده از گاز بیاثر آرگون و یا استفاده از گاز کربن دیاکسید CO2
- روش جوشکاری با شعله اکسی استیلن بدون نیاز به ایجاد قوس الکتریکی
نکات مهم جوشکاری لولههای فولادی استیل یا ضد زنگ
برای جوشکاری لوله فولادی ضد زنگ میبایست موارد زیر در نظر گرفته شود:
- توجه به رده و ضخامت لوله
- اتصال جوش حداکثر ۰٫۵ میلیمتر برای ضخامت دیواره لوله استیل حداکثر 15 میلیمتر
- اتصال جوش ۱ میلیمتر یا کمتر برای ضخامت دیواره لوله استیل حداقل 15 میلیمتر
- حداکثر انحراف مجاز ۱۰۰۰ / ۱ در صورت مستقیم بودن محور دو گروه لوله
پاس انواع جوش اتصالات لوله فولادی
از انواع پاس میتوان به موارد زیر اشاره کرد:
- پاس ریشه
- پاس داغ
- پاس پرکننده
- پاس پوششی
قوی ترین جوش در انواع روش جوشکاری
معمولاً با توجه به فلز و نوع کاربرد از جوشکاری قوس گاز- تنگستن یا GTAW و جوشکاری قوس گاز- فلز یا GMAW بهعنوان با کیفیتترین انواع جوش لوله فولادی نام میبرند. جوشکاری قوس گاز- تنگستن یا GTAW بالاترین کیفیت جوش به ویژه در صخامت های نازک را ارائه میدهد و در مقابل جوشکاری قوس گاز- فلز یا GMAW گستردهترین فلزات و ضخامتها را شامل میشود و بهترین تکنیک جوش کاری برای اکثر کاربردهای فولادی به شمار میرود. درنهایت انتخاب بهترین روش جوشکاری به نوع فلز، ضخامت، کاربرد و ... بستگی دارد.
سخن پایانی
عملیات جوشکاری یکی از بادوامترین روشهای اتصال لولههای فولادی در صنعت به شمار میرود. این روش اتصال انواع متنوعی دارد که دو روش جوشکاری قوس گاز- تنگستن یا GTAW و جوشکاری قوس گاز- فلز یا GMAWاز پرکاربردترین و باکیفیتترین آنها هستند.